The brave new world of managing cost escalation risk in the USA
The post-pandemic new normal is upon us. For large project owners, it’s presenting a toxic mix of higher interest rates, inflation, recessionary warning signs, supply-chain bottlenecks, geopolitical risks and worker shortages, which only exerts upward pressure on construction costs. Understanding more accurately how these drivers are impacting cost escalation is vital to help mitigate and manage financial risk in the current uncertain economic climate.
Paul Fostun, Associate Director, Cost Management, and Jonathan Elden, Director, Cost Management
Contributing to these hurdles is the notable take-off in manufacturing and industrial construction that started in 2022 – including many mega-sized, multi-billion-dollar projects. Leading the way are computer chip manufacturers, electric vehicle battery plants, solar-power manufacturing plants, liquefied natural gas exporting facilities, and hybrid and electric vehicle manufacturers. We are also seeing tremendous growth across sectors such as life sciences, power and utilities, and data centres to support advancing digitalisation.
Further pressure on construction costs is coming from manufacturing companies who are opting to shift production back to the United States, especially as the CHIPS Act (which boosts domestic research and manufacturing of semiconductors) and the Inflation Reduction Act have incentivised those moves. Despite challenges in sectors like corporate office and residential, the medium- to long-term construction growth story in the United States remains intact.
Wild card construction costs
At a time like the present, with mounting risk, how then are construction costs (driven by materials, labour and equipment) still wild cards when it comes to forecasting project escalation factors? Before the pandemic, using historical market-escalation factors was considered a reliable way to go, and 5 percent per annum was widely accepted as the general escalation factor.
Recently published construction cost indices bring to light the current volatility in cost escalation:
- The DGS California Construction Cost Index, for example, shows 2021 at 13.4 percent and 2022 at 9.3 percent
- Mortensen’s Chicago Construction Cost Index reported a 19 percent increase in 2021 and 7.1 percent for 2022
- Additionally, Mortensen’s Denver Construction Cost Index reported a 22.4 percent increase in 2021 and 7.7 percent for 2022
- For Phoenix, Mortensen’s cost index reported a 19.3 percent increase in 2021 and 9 percent for 2022.
Such findings put a fine point on the fact that historical norms are grossly out of date and unreliable.
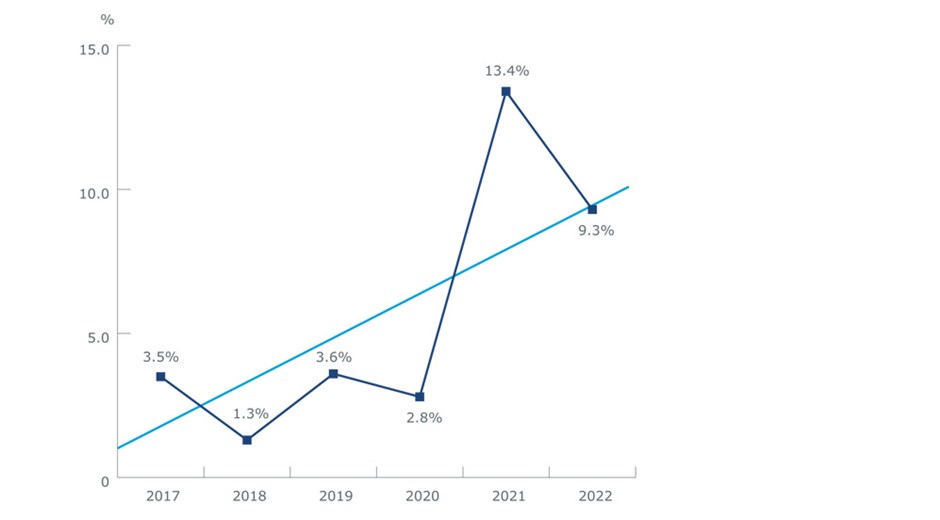
One of the greatest drivers of cost escalation relates to how the construction industry is responding to uncertainty. To shield themselves from volatility, industry players (general contractors and subcontractors) are excluding escalation fluctuations on certain trades, which only exposes their clients to the pricing risk they refuse to take on.
A new approach to forecasting
For owners with large portfolios, including mega projects, knowing how to manage cost-risk has become an urgent priority.
In our experience – and based on demonstrated results – an updated and more targeted approach is needed to establish realistic escalation targets and reduce the risk of leaving money on the table or over inflating budgets.
When it comes to forecasting costs, we have seen both sides of the coin. There are instances where forecasted escalation has been greater than the actual escalation, and money has been left on the table. This money (millions of dollars) wasn’t returned to the owners until the end of the project and could have been reinvested in other projects or in early research and development.
On the flip side, we have seen more situations where the forecasted escalation is lower than the actual escalation, which resulted in the need for cost-cutting measures, reducing the scope and/or quality of a development, and requests for extra funds from leadership to maintain project scope and/or quality.
Both scenarios can wreak havoc for large portfolios. So what are some solutions?
Forget the status quo: look back to look forward
Instead of accepting the status quo, owners of large projects or portfolios should adopt a detailed methodology that leverages current data and benchmarks to increase accuracy in the escalation forecasts and costs – and ultimately mitigates risk factors.
Data is key, but how it is analysed and used is what really counts.
The right data considers the unique cost drivers of a real estate portfolio, which leads to more educated predictions of actual escalations and costs, more precise cost forecasting, and strengthened confidence in escalation and risk factors. This may include data on labour costs, material prices, transportation costs, and other factors that could impact the overall cost of the project.
The 80/20 rule also comes into play. By focusing on the 20 percent of the overall construction cost mix that makes up 80 percent of the cost, owners can achieve more targeted prediction results that, in turn, can save money and reduce risk.
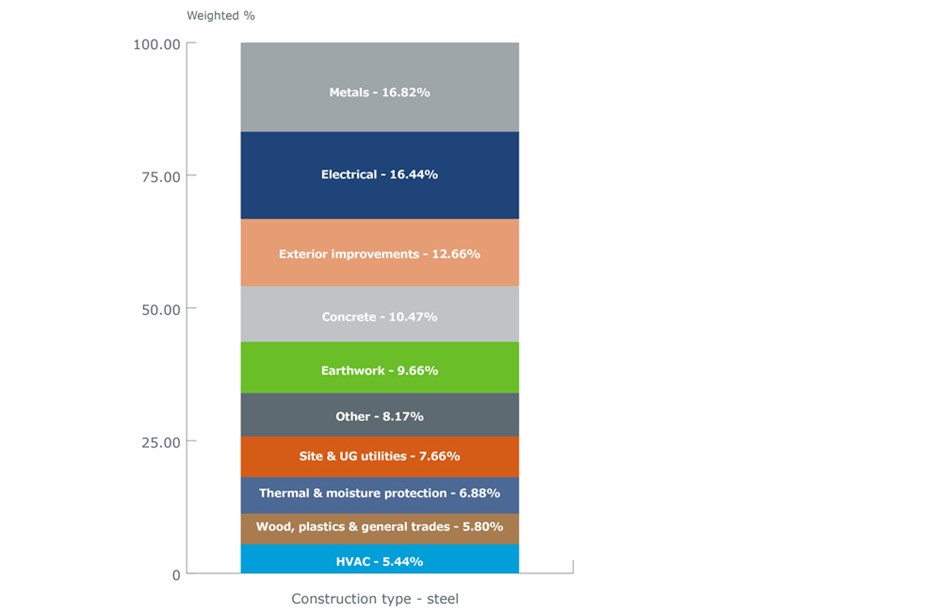
Following a data-driven, detailed approach to a large real estate portfolio and combining it with industry reports and supply chain insights will provide increased confidence in escalation forecasts.
Of course, the underlying factors that affect a company’s real estate portfolio differ from portfolio to portfolio. That’s where knowing the 20 percent of the items that make up 80 percent of total costs is important when determining the escalation and risk factors for a specific real estate portfolio.
Take control
To gain better control of construction costs and risk in the market during 2023 and beyond, an owner should:
- Start by understanding your business’s own, unique historical escalation data. A detailed, historical look back allows for a data-driven look forward. Focus on the 20 percent of the items that make up 80 percent of your costs
- Collaborate with the supply chain, from consultancies to general contractors and subtrades. The human aspect must always be taken into consideration and understanding what the market is ‘saying’ is essential to forecasting escalation costs
- Assess what you will be spending money on for the duration in question and identify the key drivers by reviewing which trades have a significant impact on your portfolio or project(s) and understanding the underlying commodities and labour associated
- Understand the risks, trends and projections associated with these key drivers to feel more confident that the resulting escalation rate is applicable to your portfolio. Do this by looking at historic data, understanding when your portfolio or project is planned to commence and listening to the industry about any short-term risks
- Rely on proper data analysis and interpretation by allocating resources in-house or seeking advice from cost, construction and data experts.
In the current uncertain economic climate, implementing a detailed escalation methodology that leverages current data and benchmarks is vital to increase cost escalation forecast accuracy, thereby mitigating risk. Those with better control of construction costs and risk in today’s market have a greater chance of success.